SAWMILLS SHOULD ASK THESE BEFORE PURCHASING SCAN HEADS
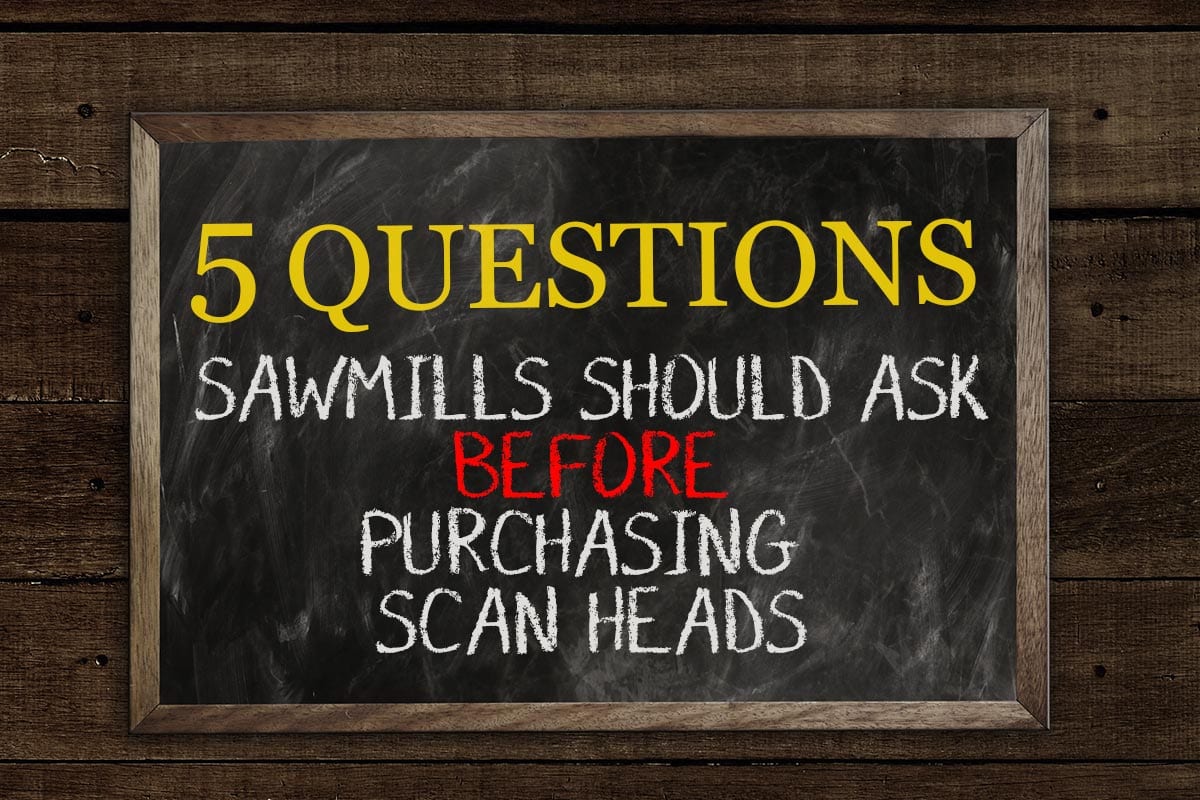
Asked and Answered by our resident Sawmill Scanning Expert Joey Nelson, JoeScan Founder & President
When your sawmill decides it’s time to install or upgrade an optimization system, give careful consideration to the scan head component.
Scan heads are an integral part of every optimization system, and it’s crucial that you ask questions about the scan heads before you select an optimization system.
The technical specifications and capabilities are obvious factors in selecting a scanner; however, you should look beyond the tech specs and ask both scanner manufacturers and their end users these five key questions before you purchase any scan heads.
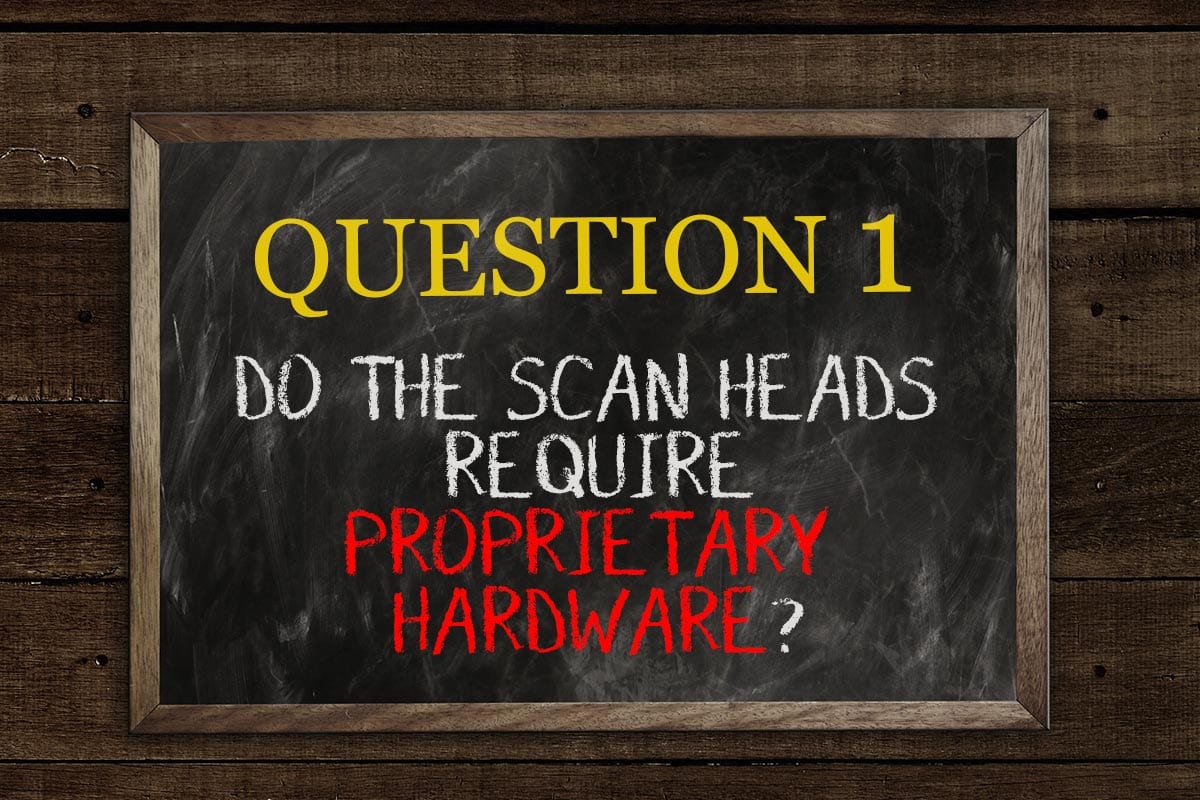
Many scan heads will require additional proprietary hardware to operate within your optimization system.
Consider the investment required to purchase dedicated hardware, and whether your mill will also need to buy spare hardware as a backup. Proprietary hardware can create obsolescence issues, so ask about the useful life of the hardware, and how long the manufacturer will commit to supporting it. There’s no industry standard for hardware requirements – they vary by scanner manufacturer, so it’s important for you to research these factors ahead of time.
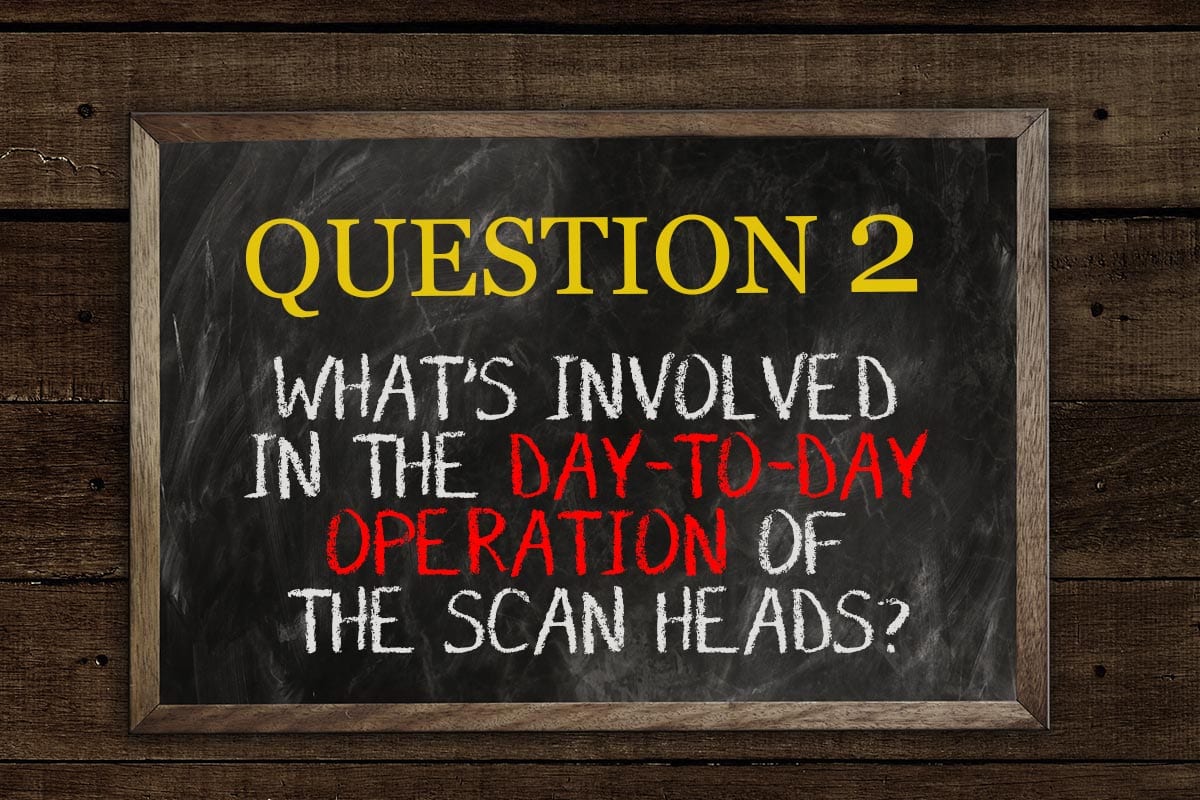
Talk to end-users and the system integrator about how easy the scan heads are to use.
Remember: Once you’ve installed the system, the system integrator goes home and you’re responsible for the day-to-day operations and maintenance. For example, calibration is a critical aspect of scanner operation. Consider the process involved to calibrate the scan heads, the skill level involved, and how often they require re-calibration. Does re-calibration require an engineer or an electrician, or can an operator do it? The answers to these questions make a big impact on your day-to-day ownership experience.
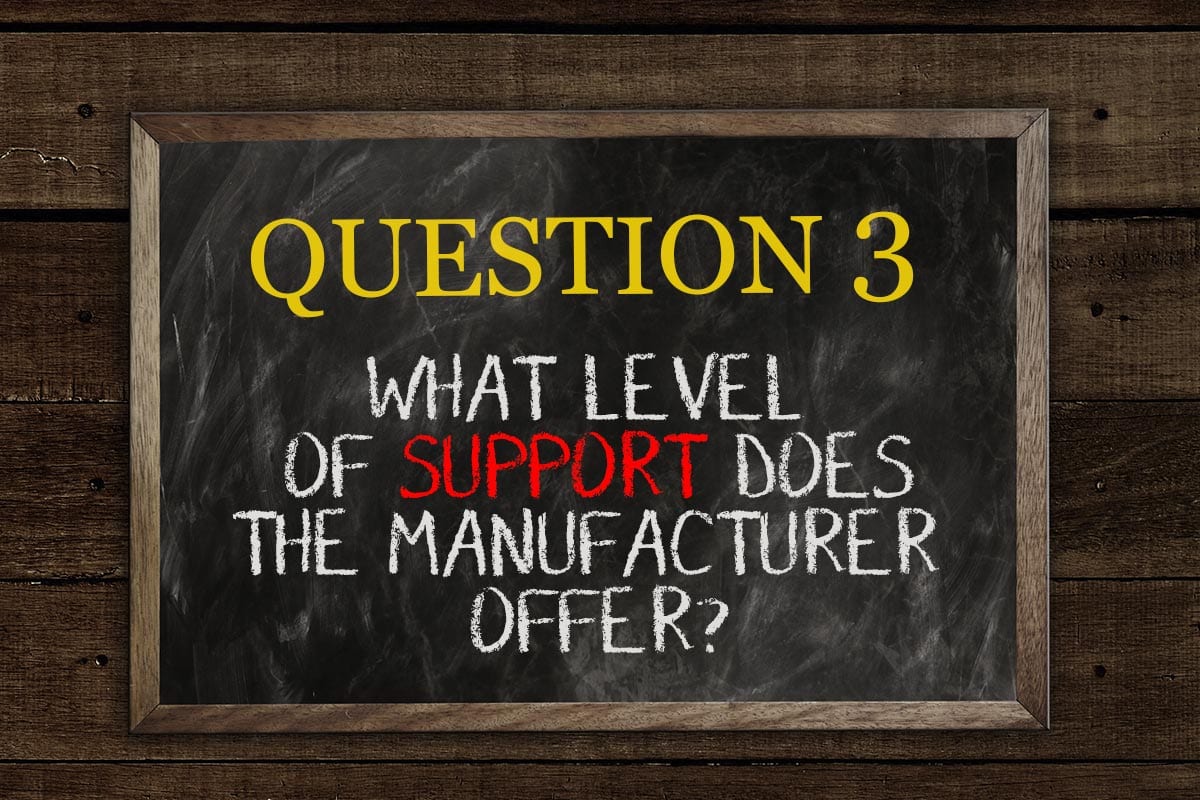
Troubleshooting is time-consuming, which ultimately impacts your mill’s bottom line.
Inquire about the level of support the scanner manufacturer offers, as well as who within the company provides that support. The manufacturer’s depth of knowledge is also important – does the company have specific expertise in the sawmill industry?
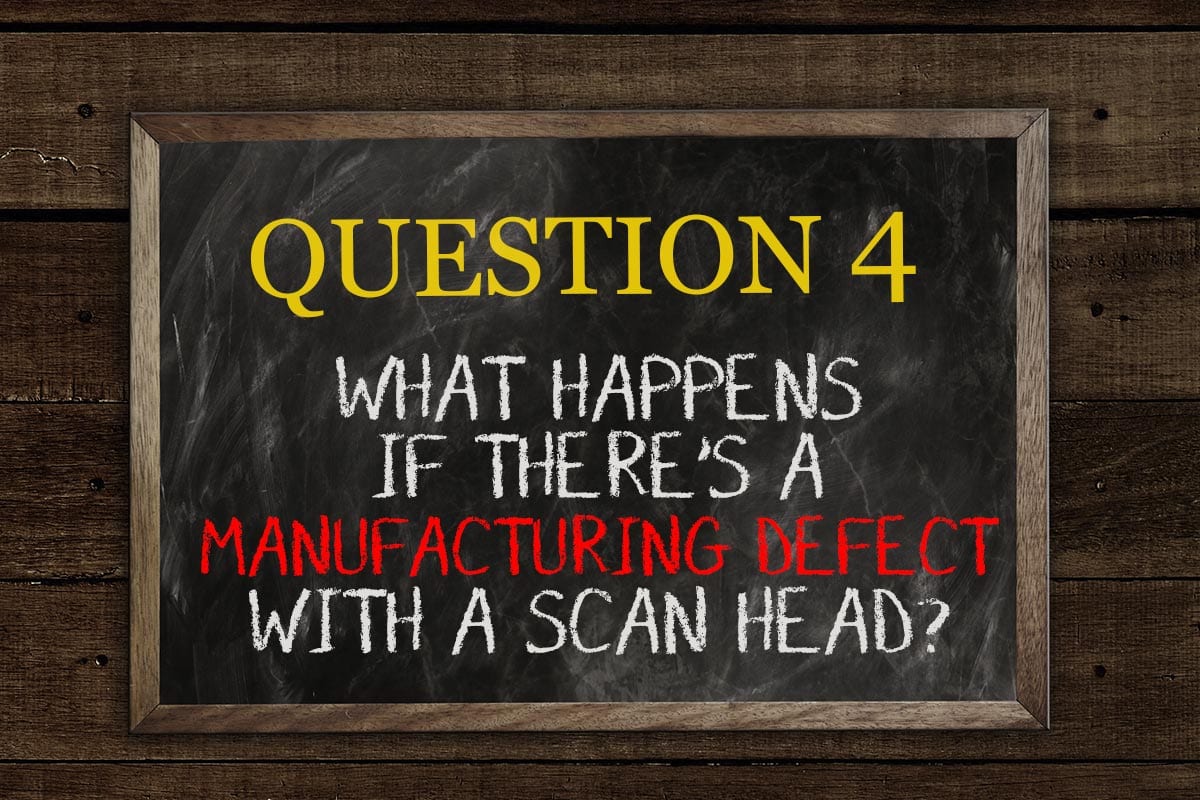
Consider whether the manufacturer offers a warranty, and the length of that warranty.
Warranty coverage differs significantly between manufacturers, so carefully review the terms of the warranty and what it covers. And don’t forget to ask for historical data regarding turnaround times for shipping back repaired or replacement scan heads.
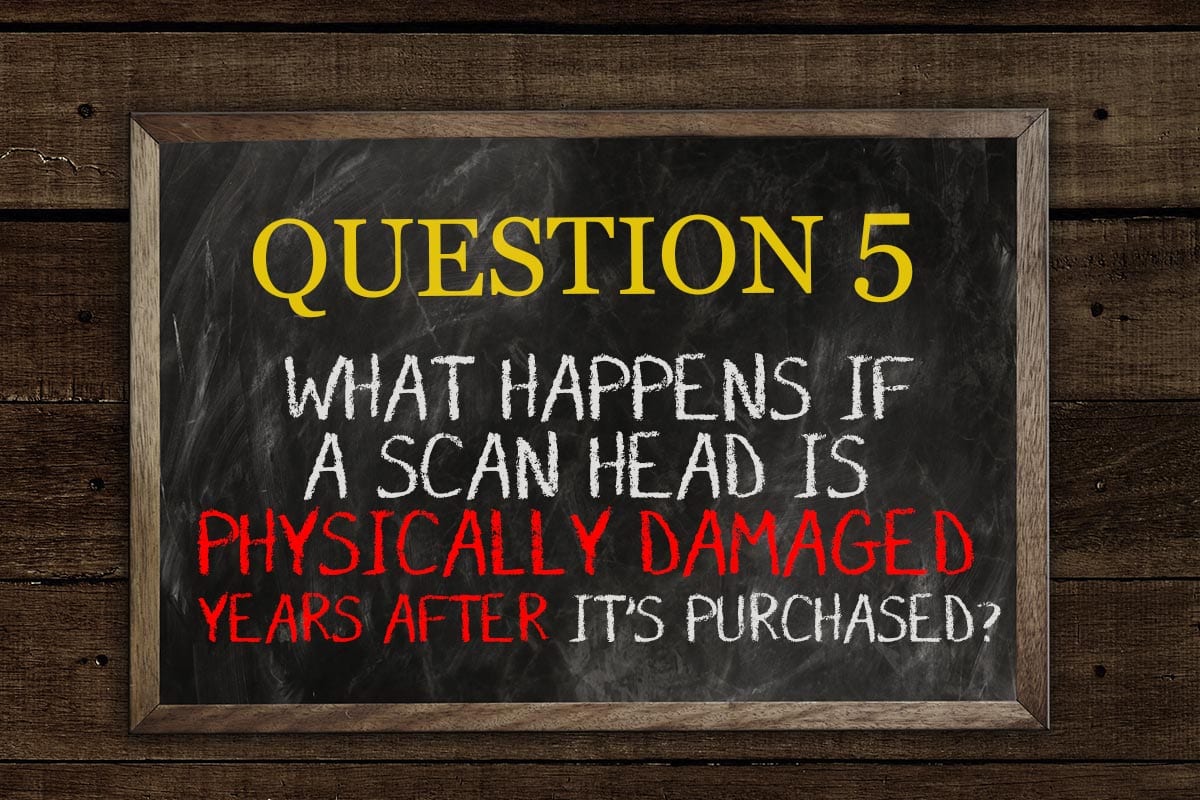
In the harsh environment of a sawmill, sometimes equipment gets broken.
Consider how long the manufacturer supports its product, and the time frame before that product becomes obsolete. Investigate a scanner manufacturer’s average turnaround time on repairs.
Ask whether the manufacturer has a minimum repair cost, and whether it caps the maximum repair cost. These considerations factor into the overall cost of ownership and the longevity of your mill’s investment in scan heads.
SHOP AROUND
Product offerings vary widely across the scanner industry.
You should look beyond the technical specifications to the value-added benefits of the equipment and manufacturer. Talk thoroughly with scanner manufacturers, and their end users, to make an informed decision. Ultimately this approach lowers your overall cost of ownership. Best of all, it boosts your mill’s productivity and increases its bottom line.
MORE QUESTIONS?
If you need answers to these, or any other questions you may have about 3D laser scanning in sawmills, we’re here to help!
We do check the comments so please feel free to leave one below.
You can also reach out to us at joescan.com/contact and we’ll get right back to you.
Leave A Comment
You must be logged in to post a comment.