LESSON 1: BUCKING & MERCHANDISING
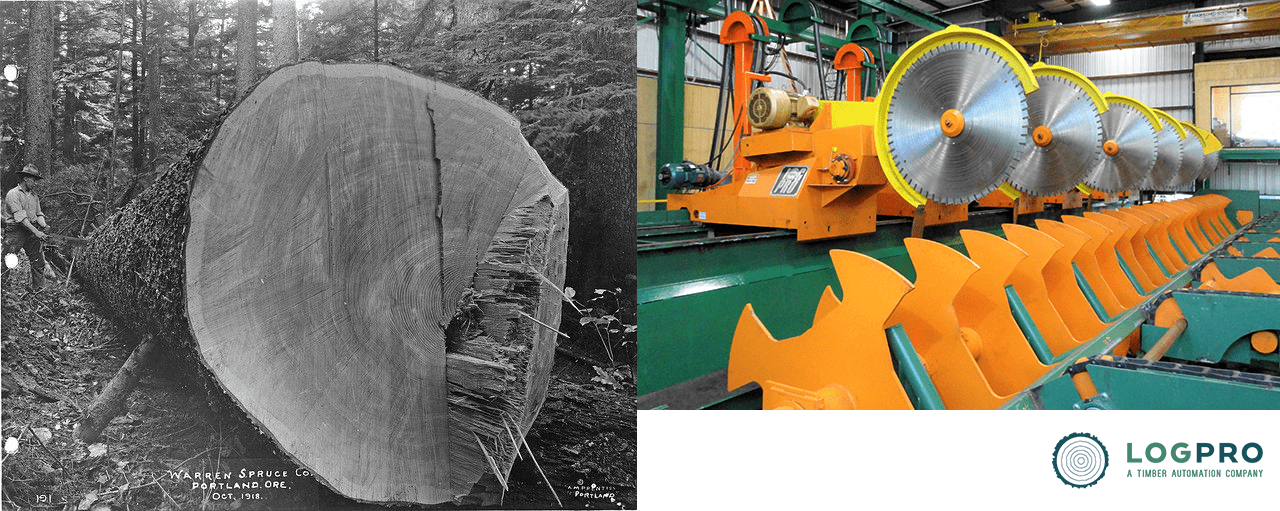
We’ve come a long way in bucking systems.
Bucking, or merchandising as it’s sometimes called, is the process of cutting tree-length stems into manageable lengths so that they can be fully processed further down the saw line. How and where to cut these stems is the first decision that most sawmills need to make. As such, it’s a critically important decision, because everything else that happens down the line depends on these first cuts.
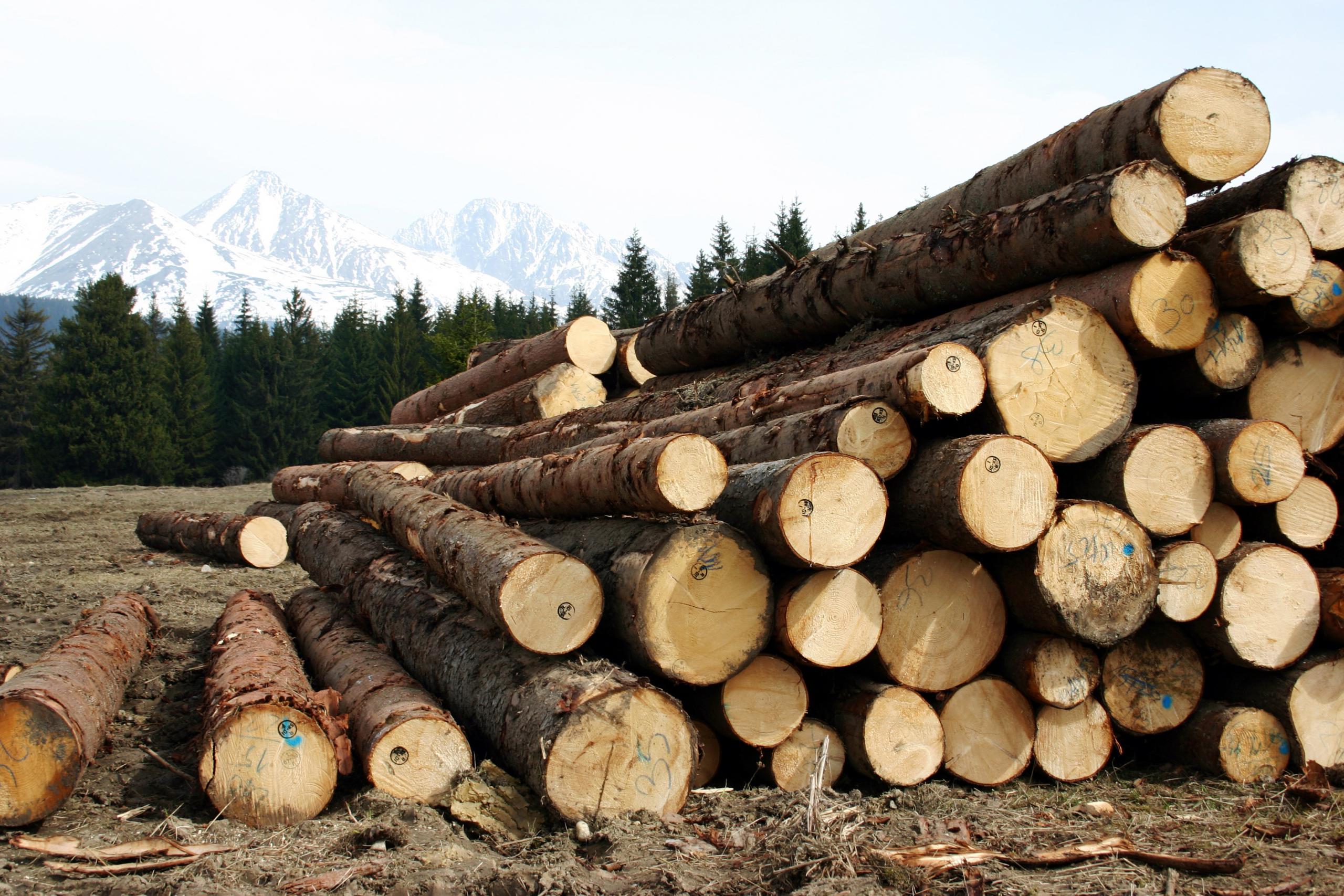
STEMS
Up to tree-length boles. De-limbed sections of the trunk of a tree. They are what arrive on logging trucks.
After bucking, the individual pieces are called logs.
Bucking Optimization Overview
Stems need to be debarked and cut into lengths the rest of the mill equipment can handle. This choice of what lengths to cut a stem into may seem simple at first glance. The lengths need to be:
- short enough for downstream equipment to process
- long enough to produce valuable and salable lumber
As in all optimization, a major goal for bucking is to maximize profit of the mill as a whole. To truly achieve this goal is one of the most complex optimization tasks in the entire sawmill industry. When a full dollar-driven optimization is attempted, the parameters can be very complex and make it difficult to configure. In effect, bucking optimization is an attempt to simulate the entire sawmill. This simulation is then used to estimate processing costs and the value of the final lumber.
Most bucking optimizers tend to take a less aggressive approach. A common issue caused by bucking is to end up with a poor mix of product lengths. Many mills instead go with simpler heuristics that ensure a good mix of lengths. These simpler systems are easier to adjust and tweak. For larger mills with multiple cutting lines, the bucking system also sorts which line a given log will be sent to. This sorting is most often based upon stem diameter and sometimes sweep characteristic.
SWEEP
The natural curve along the central axis of a stem. Most species of timber-producing trees exhibit at least some sweep.
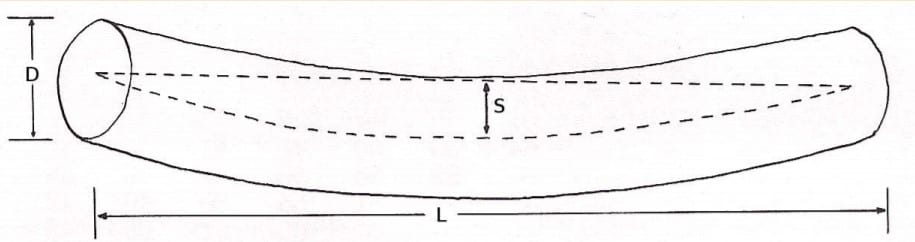
Sweep (S), diameter (D), and length (L) of a stem.
Image via Log Evaluation and Grading, Ed Thomas & Neal Bennett, USDA Forest Service Forest Products Laboratory
Scanning on the Bucking Line
The scanning for bucking systems is ideally done after the bark has been removed from the stem, so you are measuring the geometry of the good fiber. There are three ways a stem is typically scanned:
- lineal
- snapshot
- transverse
These three approaches are used throughout the mill, but we will first cover how they apply to bucking optimization.
Lineal Scanning
Scanning that is performed as wood travels parallel to the grain.
Example on a lineal edger.
Snapshot Scanning
Scanning that uses multiple sensors to scan wood that is not moving.
Example on a carriage.
Transverse Scanning
Scanning that is performed as wood travels perpendicular to the grain.
Example on a trimmer.
Lineal Scanning on a Bucking Line
This is the most common type of scanning for a bucking line. Here’s how it works:
The log is placed on a chain or a belt. The chain or belt moves the log lengthwise through a scanner. The scanner typically consists of 3 or 4 laser profiling scan heads. This is a simple system and can be very effective.
It does require a long transport chain or belt, greater than twice the length of your longest stem. Sometimes the mill property layout makes this difficult or cost prohibitive. Additionally, it requires a lot of steel to support the log through the scan zone.
In some cases this can be addressed with a multi zone scanning system. In a two zone system one zone is responsible for scanning the leading half of the stem, the other from the trailing half. The difficulty with multi-zone scanners for bucking is that it typically means the log needs to enter from the size of the zone. The scan frame needs to be C shaped. It is difficult to shield sunlight from a system like this. However if the bucking system in a fully enclosed building this can be a great option.
Another challenge is that a lineal scanning system typically uses an encoder measuring the chain or belt travel. Therefore it is important the stem doesn’t slip. If the stem can slip on the transport, then an additional technology will be needed to make accurate length measurements.
Snapshot Scanning on a Bucking Line
Bucking scanning can also be done with a snapshot type scanning system, which measures the log without moving. This can either be done with a large bank of profiling sensors, or with a flying spot time-of-flight sensor.
A snapshot scanning system reduces the length of the transport necessary, which can make it a good fit for upgrades to existing non-optimized bucking lines.
Transverse Scanning on a Bucking Line
Finally, there is the possibility of transverse scanning of stems. It doesn’t appear that this is being done in sawmills today.
However, it would give good length measurement. In many cases it would require scan heads that could operate in at least partial sunlight. There are also challenges with the transverse transport. If the log is not well supported and sections are bouncing as it is scanned, this will lead to poor measurements.
Bucking in the Forest & Sorting
In many parts of the world, trees are bucked in the forest. This is typically done without any scanning and optimization, although there are existing portable bucking lines for this purpose.
One advantage to optimized bucking in the field would be that different parts of the same log could be sent to different customers. In these cases the sawmill typically receives specified length logs. Often these logs are scanned as they are offloaded from the trucks. The results of this scanning can be used to audit the log suppliers.
Additionally in many cases this pre-bucking scanning is used to sort the logs according to specific cutting patterns. This allows the mill to set the machinery to a fixed cutting pattern and run with minimum gap between logs. If the logs are coming in for bucking randomly, then you might have a small log followed by a large log, and the saws will have to move substantially between the two logs. You must leave enough gap between logs to ensure that the saws are in position before the next log enters. Often this gap is set by the worst case, which means you have significant time when the machine is cutting air.
Leave A Comment
You must be logged in to post a comment.